La fraiseuse CNC
A l'origine, Sebastian End n'avait besoin que de découpes de bois parfaitement identiques pour un haut-parleur. Il a ensuite commencé à construire une fraiseuse CNC.
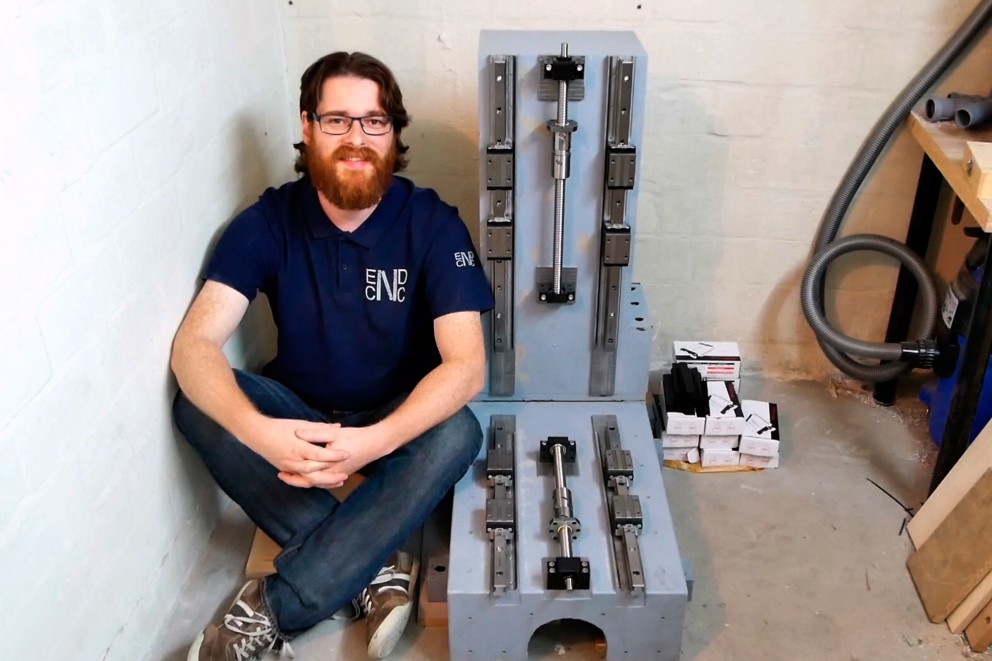
Les bonnes idées viennent souvent quand on s'y attend le moins. Sebastian End était en train de construire un haut-parleur. Il avait besoin d'une grande quantité de découpes de contreplaqué parfaitement identiques. Pour ce faire, il a commencé à monter sa première fraiseuse. Son projet s'est vite transformé en nouveau hobby. Il y a deux ans, il s'est dit qu'il pouvait améliorer sa fraiseuse CNC et il a commencé à en fabriquer une nouvelle, qu'il a baptisée «Elke».
Il s'est mis au travail. Il a dessiné des esquisses, qu'il a ensuite examinées avec soin. Quelles devaient être les capacités d'«Elke»? Il rêvait d'un asservissement de broche, d'un changement d'outil automatique et d'avoir la possibilité de tarauder des pas de vis. Il voulait aussi qu'elle soit plus stable et performante que sa grande sœur, pour qu'elle puisse travailler l'acier et l'acier inoxydable.
Il a ensuite créé son projet de CAO sur ordinateur. Il a collecté des pièces standardisées, dessiné des modèles 3D et il est allé se renseigner auprès des fabricants. Il a dû faire trois à quatre ébauches avant d'avoir les bonnes proportions et de terminer le modèle 3D.
Il a coulé les deux composantes principales dans un béton spécial lié par du ciment, puis il a attendu 30 jours que le béton «vieillisse» et qu'il se fige complètement.
Pendant ce temps, il a cherché des sous-traitants et acheté d'autres pièces de construction. Il en a commandé beaucoup outre-mer. Au bout des 30 jours, il a surfacé les parties en acier coulées dans le béton et percé les trous destinés à la fixation de la technique linéaire. Il faut être extrêmement précis, sinon la fraiseuse ne travaille pas assez précisément.
Il a ensuite soudé le socle fait de 60 kg de tubes en acier. Puis il a entamé le montage: il a positionné le socle et les premiers éléments de la fraiseuse dessus. Il a dû demander à quatre hommes de l'aider. Aucune partie ne pouvait peser plus de 150 kilos.
Pour terminer, Sebastian construit le capot de protection d'Elke Selon un profil de construction de type nut 8. Les surfaces sont revêtues de plaques en polycarbonate Macrolon. «Maintenant, je n'ai plus besoin de passer l'aspirateur dans tout l'atelier quand Elke se met au travail.» Elke est encore en construction, mais elle sera bientôt terminée, et Sebastian pourra l'utiliser pour fraiser les pièces d'autres projets... peut-être son haut-parleur, qui sait? Il n'a pas encore réussi à le terminer.
Texte: Catharina König | Photos: Sebastian End