Jetzt oder nie: Esther baut sich eine Werkbank
Das Herz einer jeden Werkstatt: die Werkbank. Blöd, wenn man keine eigene hat. Ständig eine mieten? Keine Lust. Unsere Autorin baut sich lieber eine eigene.
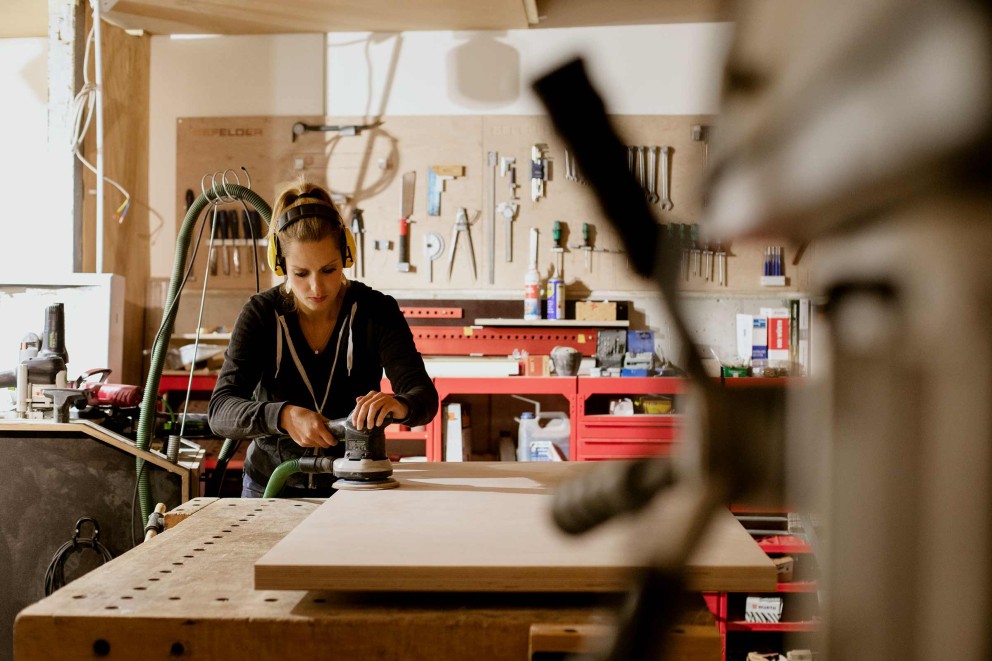
Sie war für mich da, wenn ich sie brauchte. Ist mit mir durch Projekt-Höhen und -Tiefen gegangen: Die Werkbank. Auf sie konnte ich immer bauen. Im wahrsten Sinne des Wortes. Das Problem: bisher musste ich sie mir tageweise ausleihen oder mieten. Das soll ein Ende haben. Ich will meine Projekte anpacken, wann immer ich will. An meiner eigenen Werkbank. Doch vorher muss ich sie erst mal bauen.
Jana Broxtermann
Ich rufe bei Jana Broxtermann an, die Handwerkskurse in Hamburg gibt. Unter ihrer Anleitung habe ich bereits einen Tisch restauriert. Für diesen Baukurs hätte ich sie mit ihrer ruhigen, routinierten Art gern wieder an meiner Seite. «Was meinst Du, Jana? Können wir eine Werkbank aus Holz innerhalb von zwei Tagen auf die Beine stellen?» «Das geht», sagt sie. «Aber man muss sich vorab einen genauen Plan machen, womit die Werkbank ausgestattet sein soll. Sonst verrennt man sich leicht.» Ausstattung? Einen Schraubstock soll sie auf jeden Fall haben, den braucht man fast immer. Ein Ablagebrett für kleinere Werkzeuge und Bauteile wäre klasse. Und eine Magnetplatte, die verhindert, dass Schrauben & Co. vom Tisch rollen. Geht das? «Klar. Das ist in zwei Tagen machbar. Ich empfehle Dir eine feste Werkbank mit Stellfüssen, die ist stabiler als eine mobile. Wie hoch soll sie denn werden?» Hmmm, so hoch, dass ich mit meiner Körpergrösse von 1,75 m die Werkplatte bequem erreichen kann, ohne mich zu verrenken. Jana skizziert und rechnet. Dann stehen die Masse fest: 1500 x 800 x 950 mm. Weiter geht’s: Baumaterial besorgen, Werkstatt suchen, loslegen.
Text: Esther Acason | Fotos: Charlotte Schreiber